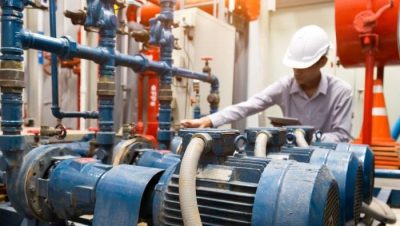
Las mediciones de vibración y temperatura de la superficie son los métodos más comunes para monitorear el estado de las bombas y otros equipos rotativos. Sin embargo, las mediciones de vibración y temperatura de la superficie del motor de la bomba o la carcasa del cojinete proporcionan solo la mitad de la historia.
¿Cuáles son las principales causas de vibración en las bombas?
Hay muchas fuentes de vibración en las bombas. Las causas más comunes incluyen ejes doblados, desequilibrios, desalineaciones, fuerzas de reacción y contacto entre componentes. Todos estos problemas pueden ser perjudiciales para la confiabilidad y el funcionamiento de los equipos rotativos.
Un aumento de la vibración puede resultar en:
- Movimiento excesivo del eje que eventualmente daña los sellos
- Hendiduras permanentes en cojinetes
- Holguras afectadas como en bujes y anillos de desgaste
- Flojedad
- Componentes dañados por fatiga
Correlacionar el control de la vibración de la bomba con la presión y la temperatura del proceso
Cuando observamos una bomba y las causas de su falla, debemos analizar más ampliamente todos sus componentes. Es importante tener en cuenta que las fallas de la bomba no siempre comienzan con cambios en la vibración y la temperatura de la superficie. Las condiciones de alteración de algunas bombas comienzan con cambios en la presión, que finalmente se traducen en vibraciones. Las fluctuaciones en las características del fluido, los cambios en la velocidad o la dirección de rotación, las obstrucciones en la descarga o la succión y los componentes internos del lado húmedo desgastados pueden causar cambios en la presión de la bomba.
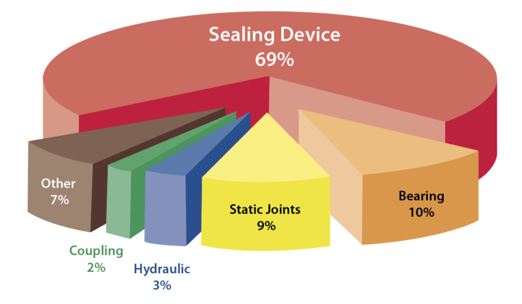
Punto de falla de la bomba n. ° 1: sellos
El primer componente más común que falla en las bombas es el sello.
Las fallas en los sellos pueden deberse a múltiples factores, muchos de los cuales no se detectan en las primeras etapas.
Algunos de los factores más comunes son los cambios de presión en los lados de succión y descarga de la bomba, que alteran directamente la presión y la temperatura de la cámara de sellado (también conocida como prensaestopas), lo que finalmente afecta al sello mecánico.
Por ejemplo: durante el funcionamiento de la bomba, un aumento en la vibración, seguido de un aumento en la temperatura del proceso de la cámara de sellado y una caída en la presión, probablemente sea causado por una restricción en el lado de succión de una bomba.
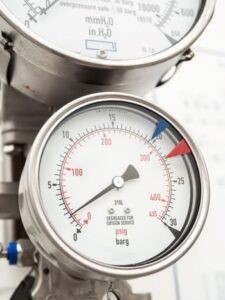
En este escenario, si solo se monitorean la vibración de los rodamientos y la temperatura de la superficie, los cambios de proceso dentro de la bomba pasarían desapercibidos. Con un aumento en la temperatura de la cámara del sello y una caída en la presión, el dispositivo de sellado (como un sello mecánico simple o un sello mecánico doble con un sistema de amortiguación) podría experimentar condiciones de funcionamiento en seco, lo que provocaría una falla prematura del sello y, en última instancia, una falla de la bomba.
Para un sello mecánico doble que funciona con un fluido de barrera, monitorear la presión y la temperatura del tanque de fluido de barrera y el fluido de proceso dentro de la bomba ayuda a confirmar el diferencial de presión adecuado, que es necesario para garantizar la lubricación y el funcionamiento adecuados del sello.
El monitoreo de la presión y temperatura del proceso combinado con la vibración puede proporcionar una comprensión clara del estado de la bomba, lo que ayuda a detectar condiciones anormales para evitar fallas y aumentar el tiempo de actividad.
Punto de falla de la bomba n. ° 2: cojinetes
Los segundos componentes más comunes que fallan en las bombas son los cojinetes.
Por lo general, las fallas de los cojinetes son causadas por la corrosión de las fugas en los sellos, el desequilibrio del equipo, la desalineación del eje, el impulsor dañado y otros. El mantenimiento de los cojinetes suele ser preventivo. Los cojinetes a menudo se reemplazan durante los reemplazos de sellos, incluso cuando aún están en buenas condiciones.
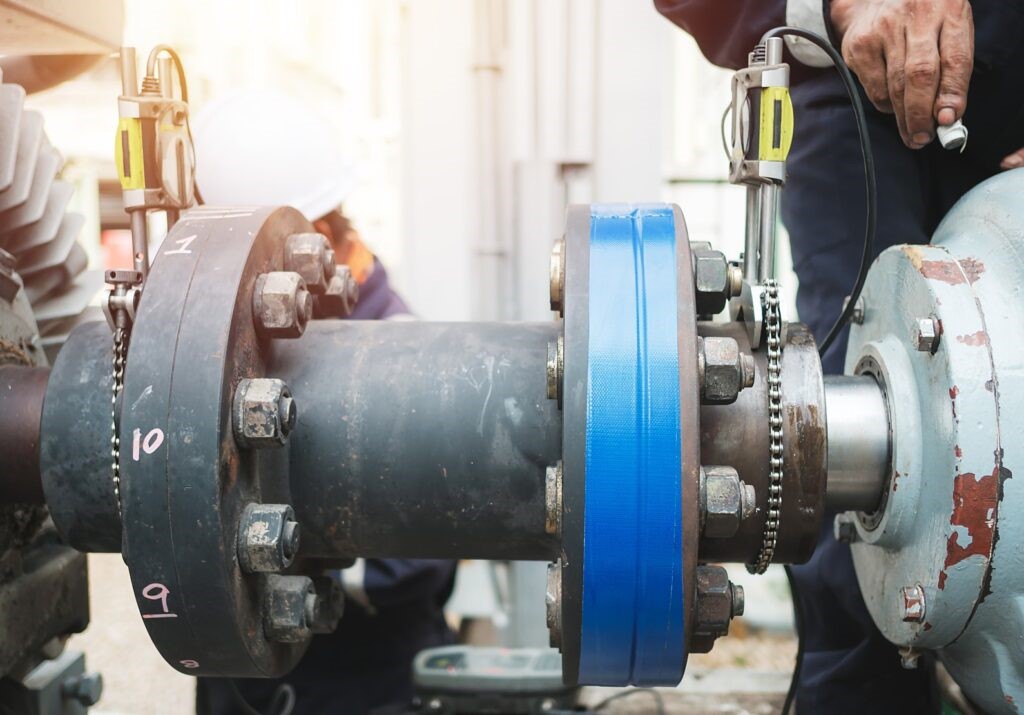
Monitoreo completo de las condiciones de la bomba
En resumen, se necesita monitorear la presión, la temperatura y la vibración del proceso de la bomba para proporcionar realmente una imagen completa y precisa del estado real de una bomba. El sensor Chesterton Connect ™ , la aplicación móvil y el análisis en la nube brindan visibilidad las 24 horas del día, los 7 días de la semana de la condición de un equipo en las cuatro áreas (presión de proceso, temperatura de proceso, vibración y temperatura de la superficie) para permitirle identificar problemas temprano y hacer correcciones en general. mayor confiabilidad y mejor desempeño de la planta.
Los siguientes son estudios de casos que demuestran cómo se usó el sensor Chesterton Connect para monitorear la presión, temperatura y vibración del proceso, brindando información crítica para el ahorro de equipos.
Estudio de caso n. ° 1: Identificación de condiciones de funcionamiento en seco

Una planta química estaba experimentando un número inusualmente alto de fallas en los sellos mecánicos de un solo cartucho en una aplicación de bomba de transferencia de ácido nítrico al 65%. El tiempo medio entre reparaciones (MTBR) fue de solo 1,2 meses.
Un técnico verificó el funcionamiento del sistema así como la instalación del sello mecánico y no encontró problemas notables en el funcionamiento de la bomba.
Nuestro especialista recomendó la instalación de un Chesterton Connect. En unos pocos días, pudieron recopilar rápidamente suficiente información para determinar que había una presión negativa en la cámara de sellado cuando la bomba estaba en funcionamiento. Esta presión negativa hizo que el sello mecánico mostrara los síntomas clásicos de funcionamiento en seco. Después de realizar una auditoría del sistema, el cliente pudo acelerar una válvula para garantizar el flujo adecuado de la bomba.
La bomba y el sello mecánico ahora funcionan correctamente y el MTBR proyectado ha mejorado a más de 24 meses. El ahorro potencial de costos de sellos mecánicos para esta bomba es de más de $ 30,000. Se estima que los ahorros debido a la reducción del mantenimiento y las mejoras operativas serán aún mayores, pero en este momento aún se están calculando.
Estudio de caso n. ° 2: bomba de refuerzo de turbina vertical
Un sello de bomba de refuerzo de turbina vertical de dos etapas falló en 2-3 días. El sello se cambió y nuevamente falló dentro del mismo período de 2-3 días. Claramente, había un problema, pero nadie sabía por qué, y era imposible «ver el interior» del sello para determinar la causa raíz del problema.

Se instaló un sensor Chesterton Connect ™ para monitorear las condiciones del proceso que causan fallas prematuras del sello. Con la aplicación Chesterton Connect, el usuario pudo registrar la presión del proceso (disminuyendo) y la temperatura (aumentando) mientras la bomba estaba en funcionamiento.
Debido a los datos de Chesterton Connect, se identificaron cambios operativos críticos y se solucionó el problema de falla del sello.
Por Juan Cid